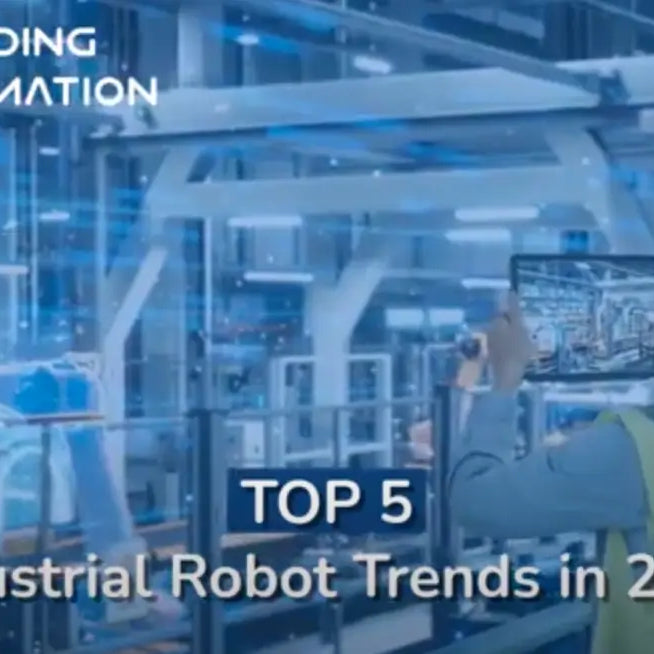
Orders & Worldwide
Orders & Worldwide
ABB ACS800 series frequency converter is a high-performance, widely adaptable AC frequency converter with a wide range of applications, advanced technology, powerful starting torque, automatic start, flux optimization, reliability and stability, and humanization With its user interface and other advantages, it is widely used in various industrial fields, such as electric power, petrochemicals, metallurgy, building materials, etc. Can control various types of motors, including AC asynchronous motors, AC synchronous motors, DC brushless motors, etc.
In the power field, ACS800 series frequency converters can be used in power plants, substations, distribution stations and other places to control the operating speed and rotation speed of power equipment. In the petrochemical field, it can be used to control the operation of pumps, fans and other equipment to improve production efficiency and product quality. In the metallurgical field, it can be used to control the operation of rolling mills, continuous casting machines and other equipment to improve production efficiency and product quality. In the field of building materials, it can be used to control the operation of kilns, mixers and other equipment to improve production efficiency and product quality.
However, during the use of ABB ACS800 series frequency converters, some problems often occur, which affect the normal operation of the equipment, such as:
These faults may affect the normal operation of the inverter and require timely investigation and repair. Different solutions should be adopted for different faults. If it cannot be repaired by yourself, it is recommended to contact professional technicians for repair
Of these two inverters, model ACS800-01-0070-7, one frequently trips and stops during operation, and reports an over-temperature alarm.
Alt: ACS800-01-0070-7 frequency
Analysis and processing:
Since the inverter was running normally in the early stage, the over-temperature alarm trip is usually caused by the inverter operating at full load for a long time and unable to fully dissipate heat. The load condition of the motor was checked to be normal, but when the inverter was removed for inspection, it was found that there was a lot of dust on the heat sink. Thick, seriously hindering the heat dissipation performance of the inverter. After sufficient cleaning and maintenance of the accumulated dust, the inverter returns to normal operation.
It can be seen from the example that our maintenance of the frequency converter is not complicated. Some common minor problems are not the frequency converter itself, but that we do not pay attention to its operating environment. Usually, the reason why the frequency converter is burned out is because these environments are not guaranteed. , caused by the accelerated aging of its internal components. Therefore, we should especially check the working conditions of the inverter during daily maintenance, including keeping the surrounding environment dust-free, water-free, corrosion-free and constant temperature. If the environment cannot be changed, regular maintenance of the inverter is very necessary.
Alt: DCS-controlled inverter
Analysis and processing:
Since the original control is normal, it means that there should be no problem with the original external wiring and control method. Check that the inverter fault code is overcurrent and overload. The possible reason is that the load is too large. According to the feedback obtained on site, there is no problem with the motor. Due to the workmanship, The change has increased the load of the frequency converter. Check that the current limit of the frequency converter is normal. Check the operating parameters during the trial operation and find that the input switch value and analog data are also normal. However, when the input analog value is about 30Hz, the output frequency is inconsistent. It turns out that the inverter's starting load capacity is obviously poor. Adjust the U/F curve to increase the voltage setting at low frequency and then eliminate the fault.
Routine maintenance methods and precautions for frequency converters include:
Routine maintenance is a key measure to ensure the normal operation of the inverter, extend its life, optimize performance, improve safety and reduce maintenance costs. It helps identify and resolve potential problems, keeping equipment running at its best and improving work efficiency and reliability.
Leave a comment