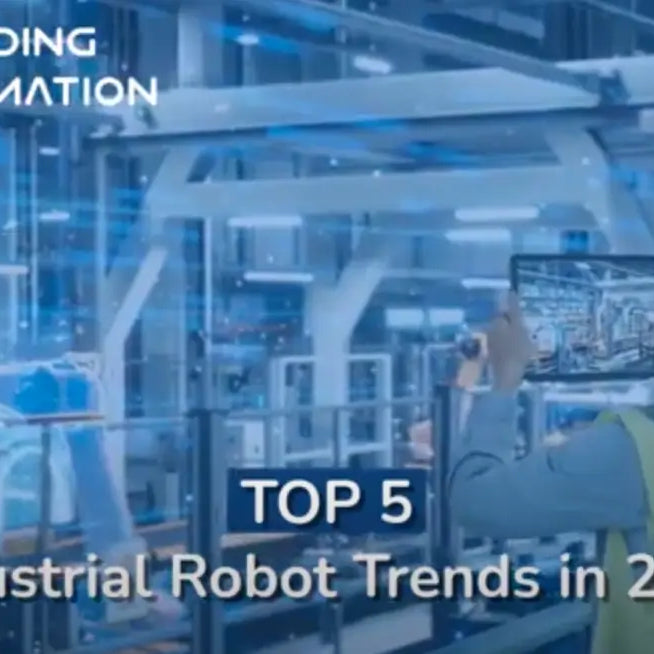
Orders & Worldwide
Orders & Worldwide
Intro
Welcome to our blog, fellow industrial robotics enthusiasts! As much as we love the incredible capabilities and efficiency of these machines, we can't deny that maintaining them can be quite a challenge. From unexpected breakdowns to wear and tear, there are various issues that can arise in industrial robot maintenance. But fear not, because in today's post, we'll be diving into some of the most common challenges and sharing practical tips and solutions on how to address them. So buckle up and get ready to learn how to keep your industrial robots running smoothly and maximize their performance. Let's go!
Regular maintenance is crucial for the optimal performance and longevity of industrial robots. One of the main benefits of regular maintenance is the prevention of unexpected breakdowns. By conducting routine checks and inspections, potential issues can be detected early on, allowing for timely repairs and replacements. Furthermore, regular maintenance improves the overall efficiency and performance of industrial robots. By lubricating moving parts, cleaning sensors, and calibrating systems, robots can operate at their full potential, ensuring smooth and precise movements. In addition, regular maintenance helps to extend the lifespan of industrial robots. By replacing worn-out parts, robots can continue to operate efficiently for a longer period. Overall, regular maintenance is essential for industrial robots to perform optimally, minimize downtime, and extend their lifespan.
Maintaining industrial robots can be a challenging task, with various issues that can arise. In this section, we will explore some of the most common maintenance challenges faced by industrial
robotics enthusiasts and provide practical tips on how to address them. One of the biggest challenges in industrial robot maintenance is unexpected breakdowns. These can occur due to wear and tear, mechanical failures, or software glitches. To overcome this
challenge, it is crucial to conduct regular inspections and routine checks. By identifying potential issues early on, prompt repairs or replacements can be made, minimizing unplanned downtime.
Another common challenge is the accumulation of dirt and debris on the robot's sensors and moving parts. This can affect the robot's performance and accuracy. To tackle this, regular cleaning and lubrication are necessary. Proper cleaning techniques, such as using compressed air or specialized cleaning solutions, should be employed to ensure the robot's optimal functioning. Additionally, programming errors or software malfunctions can lead to maintenance challenges. Keeping software up to date and conducting regular software checks can help mitigate these
issues. It is also essential to have a backup of the robot's programming and configuration settings to easily recover from any software-related problems. Lastly, another common challenge is the availability of spare parts. Industrial robots often require specific components that may not be readily available. Maintaining a well-stocked inventory of spare parts or establishing relationships with reliable suppliers can help overcome this challenge. By being aware of these common challenges and implementing proactive maintenance practices, industrial robotics enthusiasts can keep their robots running smoothly and maximize their performance.
Maintaining industrial robots can be a challenging task, with various issues that can arise. In this section, we will explore some of the most common maintenance challenges faced by industrial robotics enthusiasts and provide practical tips on how to address them. One of the biggest challenges in industrial robot maintenance is unexpected breakdowns. These can occur due to wear and tear, mechanical failures, or software glitches. To overcome this challenge, it is crucial to conduct regular inspections and routine checks. By identifying potential issues early on, prompt repairs or replacements can be made, minimizing unplanned downtime.
Another common challenge is the accumulation of dirt and debris on the robot's sensors and moving parts. This can affect the robot's performance and accuracy. To tackle this, regular cleaning and lubrication are necessary. Lastly, another common challenge is the availability of spare parts. Industrial robots often require specific components that may not be readily available. Maintaining a well-stocked inventory of spare parts or establishing relationships with reliable suppliers can help overcome this challenge. By being aware of these common challenges and implementing proactive maintenance practices, industrial robotics enthusiasts can keep their robots running smoothly and maximize their performance.
Proper training plays a crucial role in improving industrial robot maintenance. When maintenance teams are equipped with the right knowledge and skills, they can effectively troubleshoot issues, perform routine tasks, and address any challenges that arise.
Training should cover a range of topics, including the basics of industrial robotics, common maintenance challenges, preventive maintenance techniques, and troubleshooting procedures.
By understanding the intricacies of the robots they are responsible for, maintenance teams can quickly identify and address issues, minimizing downtime and maximizing efficiency. Hands-on training is particularly beneficial as it allows maintenance teams to gain practical experience in working with industrial robots. This can involve simulated scenarios or even real life maintenance tasks under the guidance of experienced trainers. By practicing maintenance procedures and familiarizing themselves with the robot's components and systems, technicians can confidently perform maintenance tasks and respond effectively to any issues that arise. Regular training sessions and refresher courses are also important to keep maintenance teams up to date with the latest advancements in robotics technology and maintenance techniques.
As industrial robotics continue to evolve, ongoing training ensures that technicians are equipped with the knowledge to effectively maintain and optimize the performance of these machines.
In summary, proper training is essential in improving industrial robot maintenance. By providing technicians with the necessary knowledge, skills, and practical experience, businesses can ensure that their robots are properly maintained, minimizing downtime, maximizing efficiency, and extending the lifespan of their robotic workforce.
Leave a comment