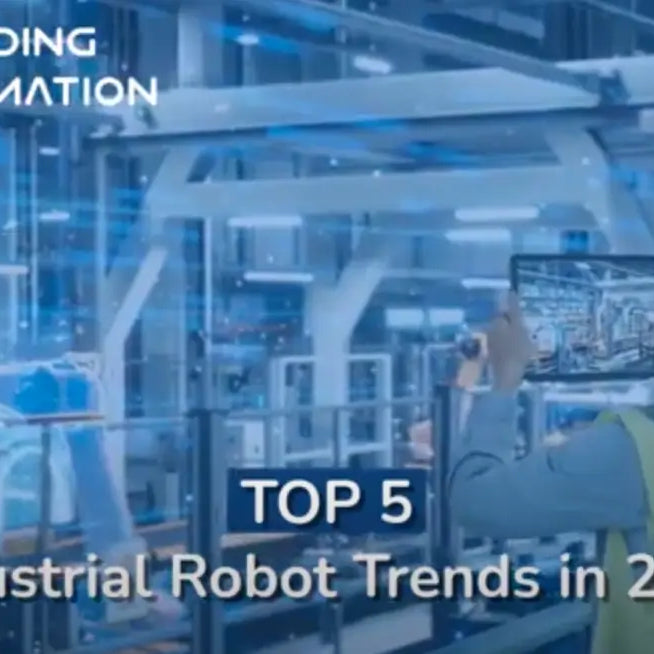
Orders & Worldwide
Orders & Worldwide
The main body of an industrial robot consists of the base and the actuating mechanisms, including the upper arm, forearm, wrist, and hand, forming a multi-degree-of-freedom mechanical system. Some robots also feature a walking mechanism. Industrial robots may have up to 6 or more degrees of freedom, with the wrist commonly having 1 to 3 degrees of freedom.
Industrial robots' drive systems are categorized into hydraulic, pneumatic, and electric based on the power source. These can be combined into a compound drive system as needed. Additionally, mechanical transmission devices such as timing belts, wheel systems, and gears can be used for indirect driving. The drive system, comprising the power unit and transmission mechanism, is responsible for the actuating mechanisms' movements. Each of these fundamental drive systems has its characteristics, with electric drive systems now being the mainstream.
Due to the widespread acceptance of low-inertia, high-torque AC and DC servo motors and their corresponding servo drives (such as frequency converters and DC pulse-width modulators), these systems do not require energy conversion and offer convenient and flexible control. Most motors are equipped with precise transmission mechanisms: reducers.
These reducers use gear speed converters to slow down the motor's rotation to the desired speed, obtaining a higher torque output, thereby reducing speed and increasing torque. When the load is large, simply increasing the servo motor's power is not cost-effective; instead, the output torque can be improved within an appropriate speed range through a reducer. The existence of precision reduction motors allows the servo motor to operate at a suitable speed, enhancing the rigidity of the mechanical system while outputting greater torque.
The control system of a robot is its brain and the primary factor determining the robot's capabilities. It issues command signals to the drive and actuating systems according to the input program and performs control. The main task of industrial robot control technology is to control the robot's range of motion, posture, trajectory, and motion timing in the workspace. It features simple programming, software menu operation, a user-friendly human-machine interface, online operation prompts, and ease of use.
The controller system is the core of the robot, and foreign companies have tightly sealed experiments in our country. In recent years, with the development of microelectronics technology, the performance of microprocessors has become higher, while the price has become cheaper. Nowadays, the market has already seen 32-bit microprocessors for 1-2 US dollars. High-performance, cost-effective microprocessors have brought new development opportunities for robot controllers, making it possible to develop low-cost, high-performance robot controllers. To ensure the system has sufficient computing and storage capacity, robot controllers now often use powerful chips such as ARM series, DSP series, POWERPC series, and Intel series.
Due to the inability of existing general-purpose chips to fully meet the requirements of some robot systems in terms of price, performance, integration, and interfaces, this has led to the demand for SoC (System on Chip) technology in robot systems. Integrating specific processors with required interfaces can simplify the design of peripheral circuits, reduce system size, and lower costs. For example, Actel Corporation integrates NEOS or ARM7 processor cores into its FPGA products, forming a complete SoC system. In the field of robot technology controllers, research is mainly concentrated in the United States and Japan, with mature products such as Delta Tau (USA) and Yaskawa Electric Corporation (Japan). Their motion controllers are centered on DSP technology and adopt an open architecture based on PC.
It consists of internal and external sensor modules to capture meaningful information about the internal and external environmental states.
Internal sensors: Sensors used to detect the robot's own state (such as the angles between the arms) are mostly sensors that detect position and angle. These include position sensors and angle sensors.
External sensors: Sensors used to detect the environment in which the robot is located (such as detecting objects, the distance to objects) and conditions (such as detecting whether the object being grasped has slipped). These include distance sensors, vision sensors, and force sensors.
The use of intelligent sensing systems enhances the mobility, practicality, and intelligence of robots. Human perception systems make robots more dexterous, and for some special information, sensors may be more effective than human perception systems.
End effectors are the components connected to the last joint of the mechanical arm, typically used for grasping objects and connecting with other mechanisms to perform required tasks. In robot manufacturing, end effectors are generally not designed or sold; most of the time, only a simple gripper is provided. Usually, end effectors are mounted on the flange of the robot's 6th axis to perform tasks in a given environment, such as welding, painting, gluing, and part loading and unloading, which require the robot to complete.
The article and images are from the internet and are copyrighted by the original authors.
{"one"=>"Select 2 or 3 items to compare", "other"=>"{{ count }} of 3 items selected"}
Leave a comment on this topi